News
“Target hoeing” –
Using robots to combat weeds in a targeted manner
Author: Georg Supper
Challenges in field robotics
Field robot “Mathilda”
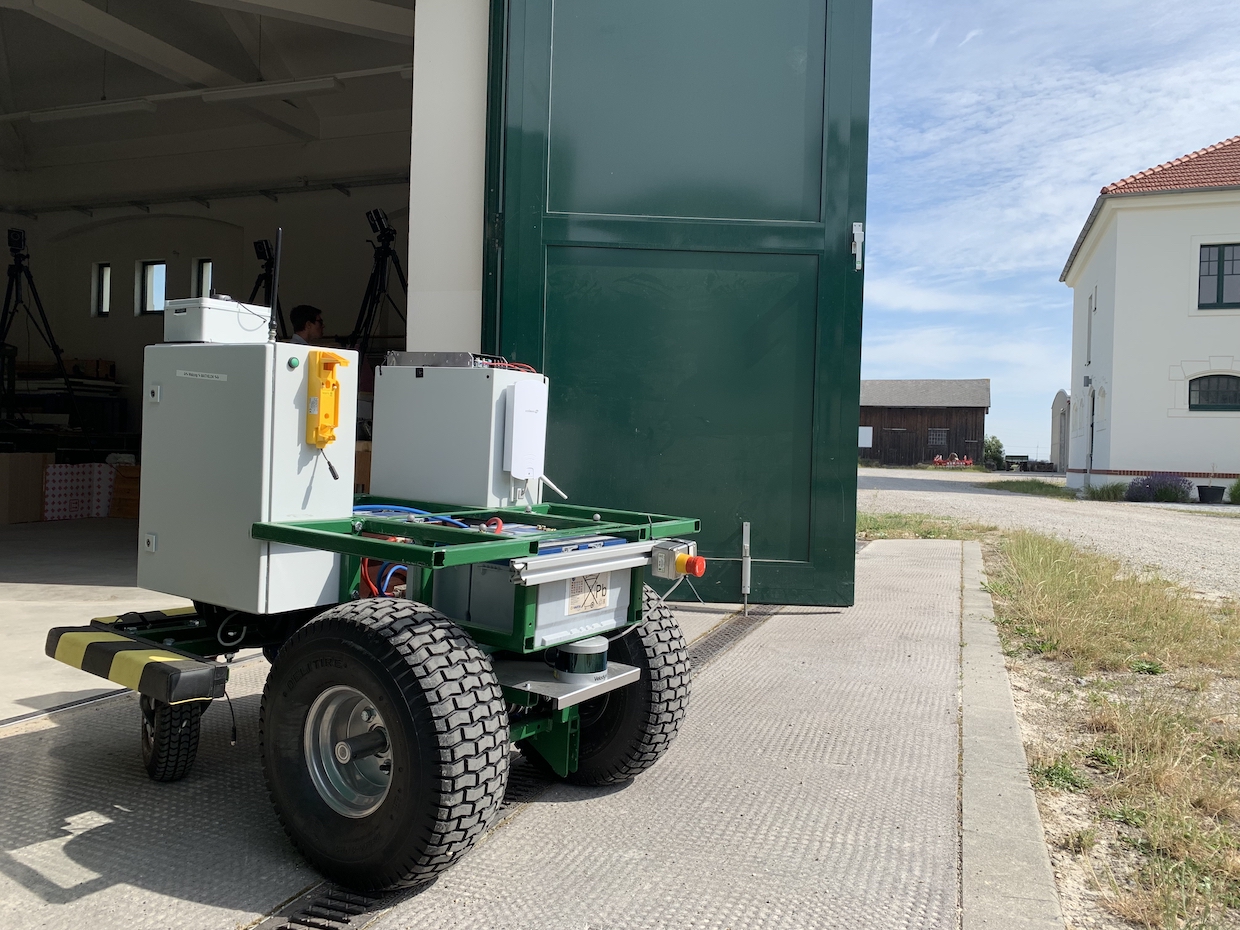
Figure 1: Field robot “Mathilda” exiting the machine test station
Development of a “Target hoe”
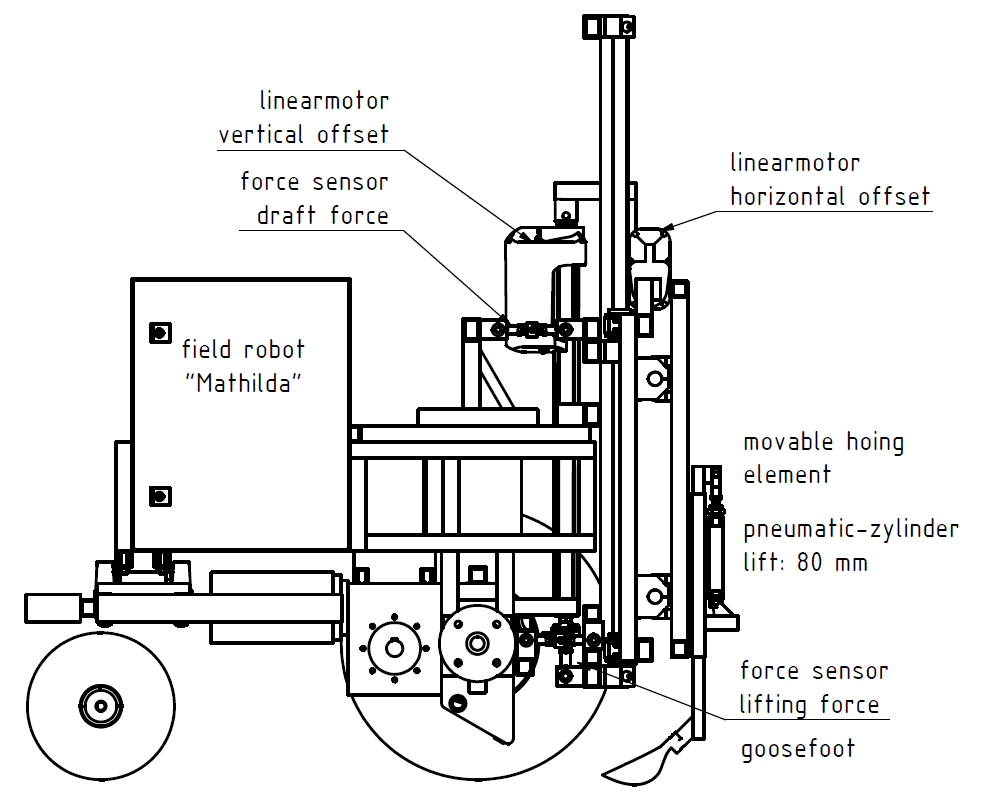
Figure 2: Illustration of the robot, the shifting frame, and the movable hoeing element
Interdisciplinary objectives and collaboration in the DiLaAg
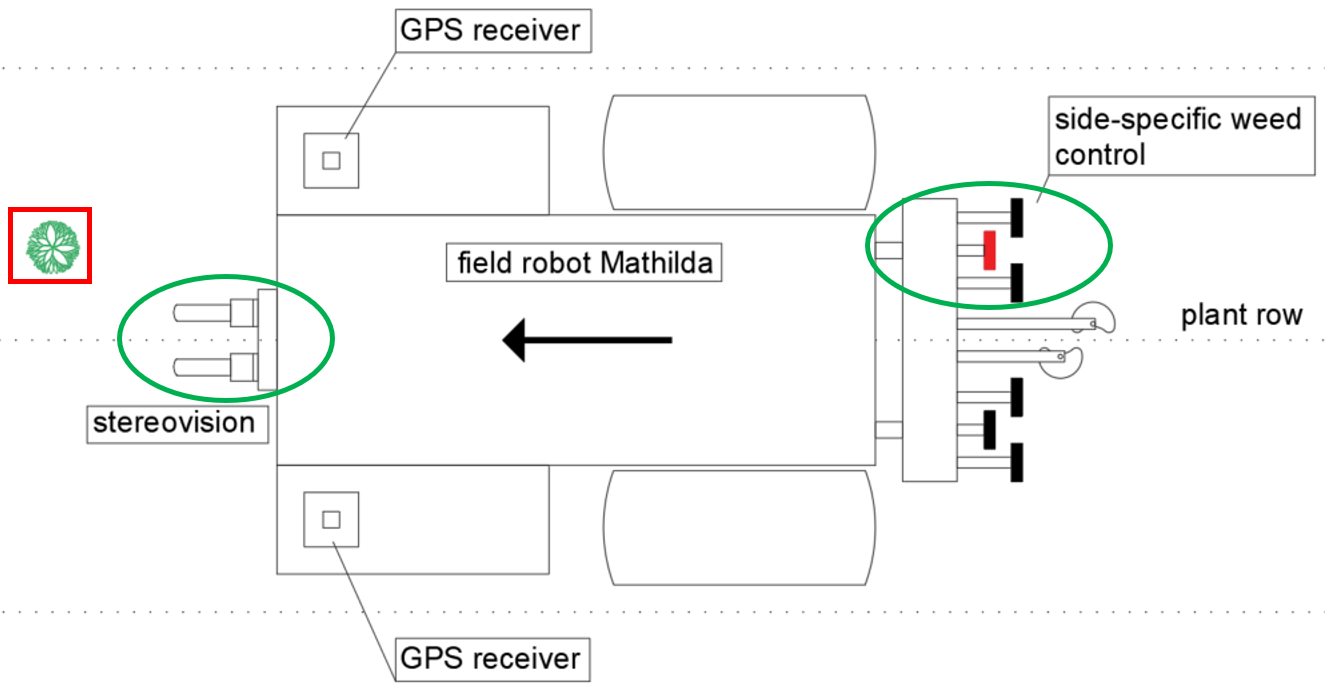
Figure 3: Schematic representation of “target hoeing”.
Cite this post as:
G. Supper, “Target hoeing” – Using robots to combat weeds in a targeted manner In: DiLaAg Innovationsplattform [Webblog]. Online-Publikation: “https://dilaag.boku.ac.at/innoplattform/en/2021/03/16/target-hoeing-using-robots-to-combat-weeds-in-a-targeted-manner/” 2020.
References:
Coleman, G. R., Stead, A., Rigter, M. P., Xu, Z., Johnson, D., Brooker, G. M., … & Walsh, M. J. (2019). Using energy requirements to compare the suitability of alternative methods for broadcast and site-specific weed control. Weed Technology, 33(4), 633-650.
Duckett, T., Pearson, S., Blackmore, S., Grieve, B., Chen, W. H., Cielniak, G., … & Yang, G. Z. (2018). Agricultural robotics: the future of robotic agriculture. arXiv preprint arXiv:1806.06762.
LINAK (2021). Linearantrieb LA36. https://www.linak.at/produkte/linearantriebe/la36/
Supper, G., Aschauer, C., & Barta, N. (2019). Planung und Entwicklung einer mobilen, autonomen Roboterplattform für pflanzenbauliche Anwendungen. 39. GIL-Jahrestagung, Digitalisierung für landwirtschaftliche Betriebe in kleinstrukturierten Regionen-ein Widerspruch in sich?.